The Environmental Diagnostics and Technology Laboratory enables the measurement, analysis and evaluation of existing and newly developed technological processes on a fractional technical scale. Due to the complexity of chemical processes and environmental issues, there is often a need for testing at the site of waste generation or production processes. For this reason, a mobile rotating fluid reactor installation with broad process capabilities, capable of operating in aggressive environments and elevated temperatures of both liquid and gas phases, was designed and constructed. The plant has a modular design and can be expanded and equipped with additional equipment to realize new technologies.
The Laboratory of Environmental Diagnostics and Technology also has chemical process analysis stations enabling in-depth analysis of processes. The main component is a real-time reaction calorimeter, which allows recording and collecting data on the course of the reaction. It allows the use of both pressurized and non-pressurized reactors.
The software makes it possible to control the operation of the reactor together with peripheral devices, monitoring and ongoing optimization of online parameters, including mixing rate, cooling, heating, dosage of reactants, etc. The software automatically records changes and modifies unit activities in the procedure. It also provides full data visualization and processing capabilities. Computer operation allows you to follow the course of a chemical reaction in a controlled and safe manner. Thanks to the vertical and horizontal arrangement of the sensor network, temperature recording is done online and in real time.
Purpose:
- development of synthesis of organic and inorganic compounds with on-line measurement of thermal effects of chemical and physical transformations in the temperature range from -50°C to 300°C
- measurement of the specific heat of the mixture during the process
- study of the distillation process with the possibility of controlling the temperature difference and the amount of distillate from the software level
- thermodynamic measurements of physical and chemical processes: flow calorimetry, real-time calorimetry, direct measurement of heat of reaction and specific heat
- process studies of crystallization, coagulation, obtaining emulsions, cosmetic creams and protein solutions
- monitoring and optimization of processes, by means of measurement of turbidity and solids content in liquids, e.g. for control of biomass growth, crystallization and filtration processes, or measurement of solids content in water purification processes
- Real-time analysis of particle size, shape, particle shape changes and the number of particles in suspension, such as in crystallization processes
- Analysis of dimensions, shape, particle shape changes and number of particles in suspension in real time, e.g. in crystallization processes
- optimization of processes by means of integration of multiple measuring devices (e.g. calorimetry + FBRM + IR + dosing systems); possibility to measure the dependence of the process flow on the conditions of the individual process steps in real time and their influence on the final process effect
- determination of reaction parameters using correlated data (calorimetry, FBRM particle size distribution, IR spectrum, zeta potential)
- development of control of the course of new processes, creation of measurement methods, control of dosing, mixing systems
- determination of thermal effects of high-energy processes
- study, analysis and development of processes for purification of gaseous streams from volatile, liquid and solid impurities, as well as operations and unit processes running at the gas-liquid interface
- conducting chemical transformations using high-performance SFR reactors in the temperature range from -20°C to 200°C and pressures from 0 to 0.2 MPa
- the possibility of conducting selected field studies
Laboratory manager:
dr inż. Robert Aranowski
View profile on:
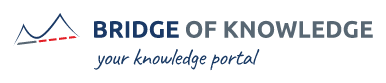